Details
Cylindrical roller bearings are widely used in machine manufacture. Through the – modified – line contact, cylindrical roller bearings can withstand a higher load than most other roller bearings of the same diameter. There are also good opportunities for using them at high rotational speeds. Compared to other roller bearings, cylindrical roller bearings have good friction behaviour. Depending on construction form, cylindrical roller bearings can also have combined – radial and axial – loadings.
The arrangement and number of boards on the outer and inner rings is crucial to this. Thus, cylindrical roller bearings can be used as floating, support or locating bearings according to their construction. To determine the permissible axial loadings, bearing geometry, roller profile and bearing size and the operational parameters of rotational speed, load and lubrication with contact surfaces must be considered. A purely axial loading of cylindrical roller bearings is not possible. Cylindrical roller bearings must be minimally radially loaded.
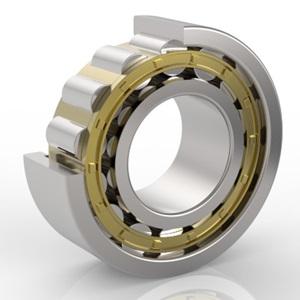
Cylindrical roller bearings can basically be distinguished by their inner construction:
Because of the higher number of rolling elements full complement cylindrical roller bearings have a higher load capacity than the same size design with cage. Because of the cage guidance cylindrical roller bearings with a cage can be used at higher rotational speed than full complement cylindrical roller bearings.
Cylindrical roller bearings with cage
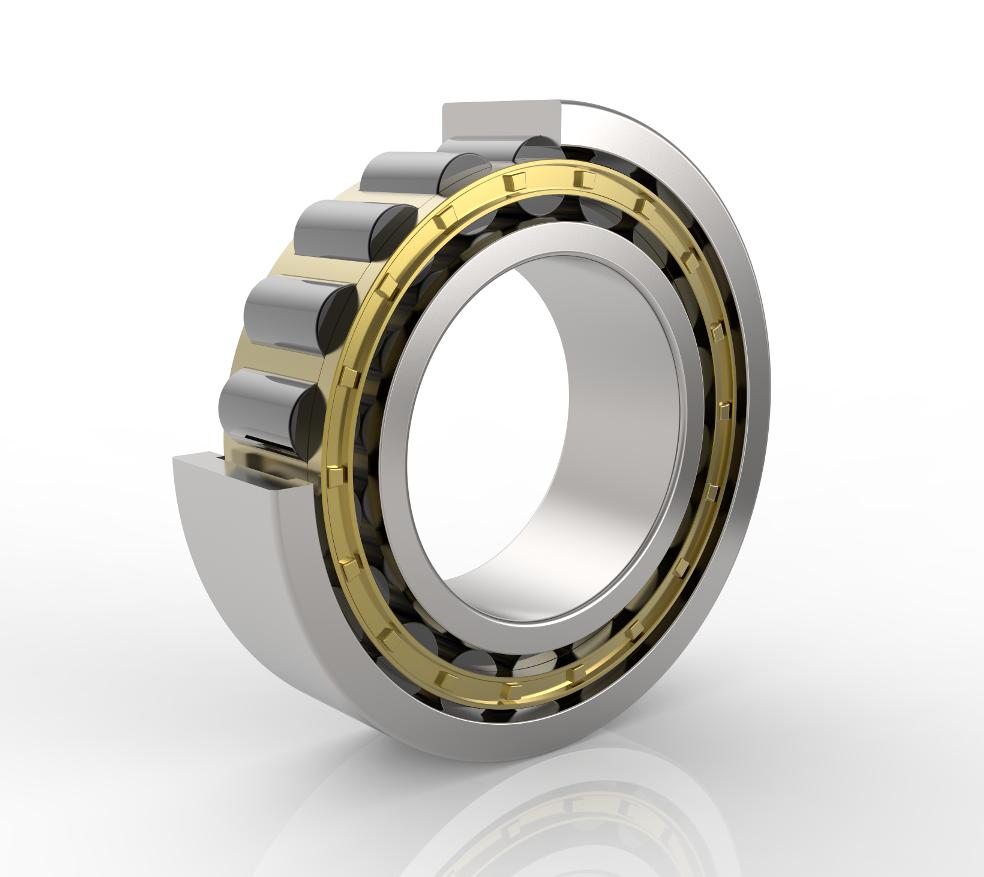
Single row cylindrical roller bearing with cage in NU design
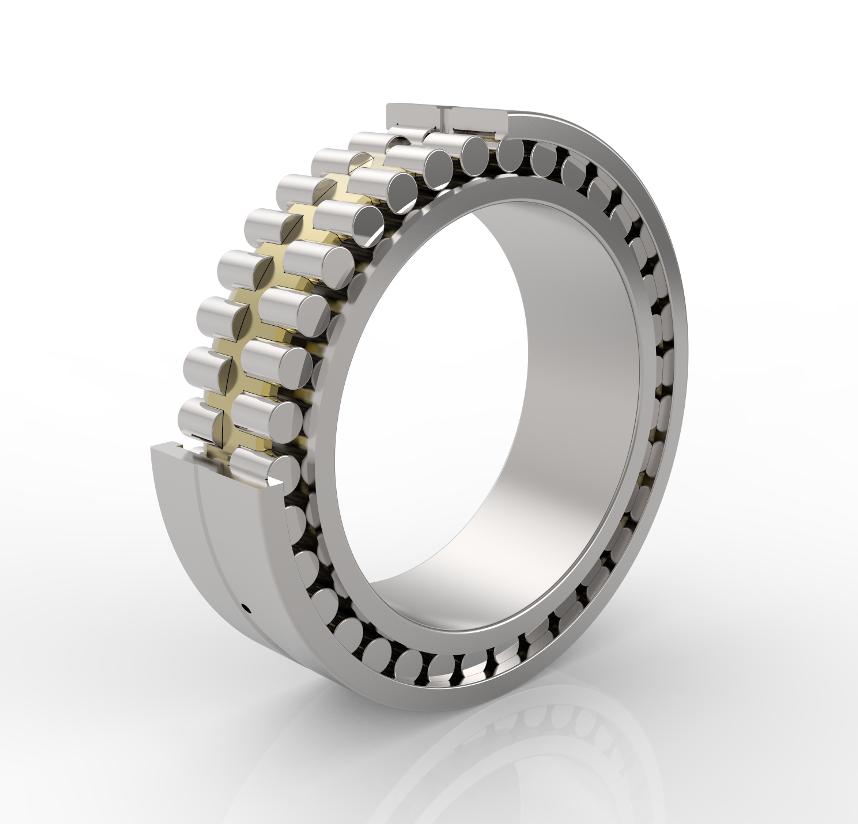
High precision double row cylindrical roller bearing with tapered bore in NNU design
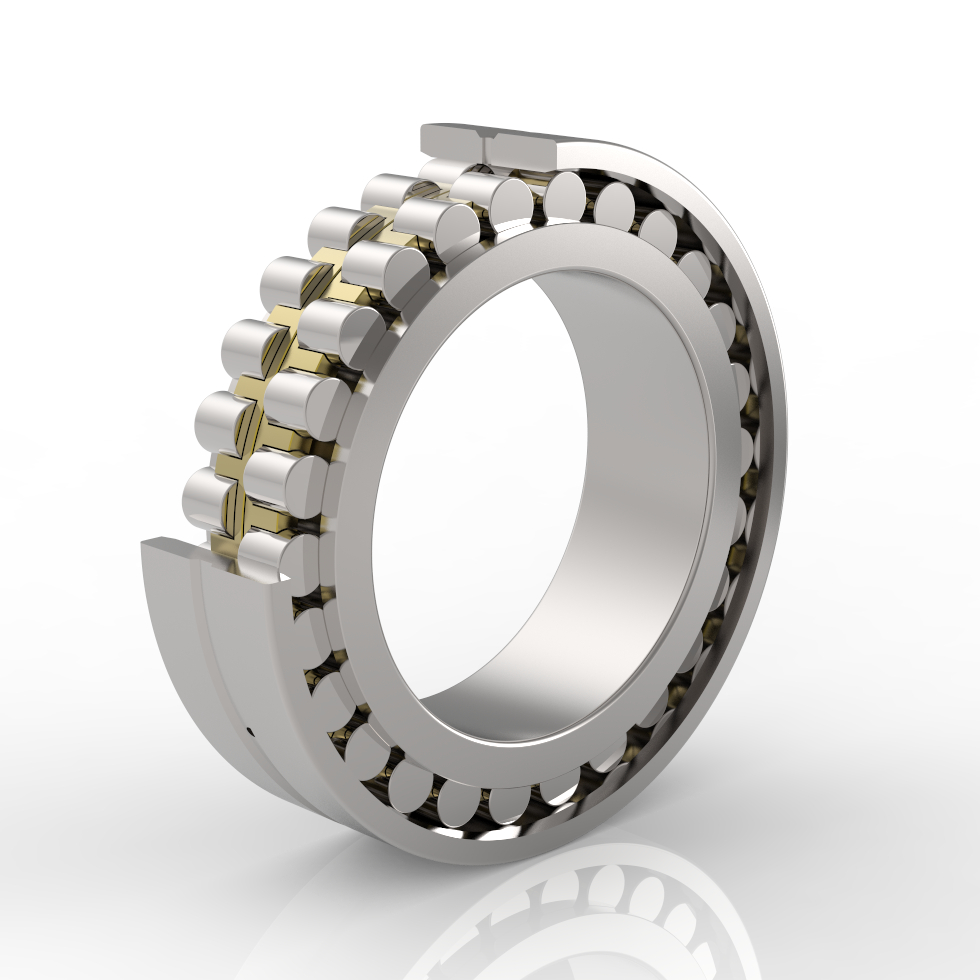
High precision double row cylindrical roller bearing with tapered bore in NN design
Cylindrical roller bearings with cage are available in a variety of designs. In all standard versions, a bearing ring (outer or inner ring) always guides the cylindrical rollers between fixed ribs. This bearing ring (marked R in front of the abbreviation) forms a coherent unit with the cage assembly. The other – loose – bearing ring (marked with L in front of the abbreviation) can be removed. Thus, in all cases, the outer and inner ring can be installed separately from each other in the adjacent construction. Both bearing rings can thereby be connected with a tight fit with the respective bearing seat, which increases the rigidity of the bearing. The one and two-row cylindrical roller bearings are mostly standardized bearings, four-row cylindrical roller bearings are special rolling bearings.
Special bearing
- Special bearings for stranding and twisting machines
- Coated bearings
- Split cylindrical roller bearings – split in axial direction
- High-precision cylindrical roller bearings with tapered cylindrical bore
- Four-row cylindrical roller bearings
- Adjustable cylindrical roller bearings
- Customer-individual constructions
Manufacture sizes
From an outside diameter of 100 mm.
Designs
- Non-locating bearing (pure radial force absorption)
- Single-row: N, NU, NB, NUB
- Double-row: NN, NNU, NNB, NNUB
- Semi-locating bearings (radial und one-sided axial force absorption)
- Single-row: NF, NJ, NU+HJ
- Locating bearing (radial und two-sided axial force absorption)
- Single-row: NP, NUP, NJ+HJ
- Double-row: NNUP
Bearing ring materials
Roller bearing steel (Standard)
Rolling elements materials
Roller bearing steel (Standard)
Heat treatments
Martensitic hardening (standard), bainitic hardening and case
Cage materials
Brass, pin type cage with perforated rollers, synthetic material
Main dimensions
–
Dimensional and running accuracy
We manufacture cylindrical roller bearings of tolerance classes normal to P4 as per DIN 620. High precision bearings with tapered bore comply with the increased tolerance class SP.
Bearing clearance
We manufacture four point contact ball bearings with bearing clearances C2, normal, C3 and C4 as per the details in DIN 628-4, up to individually limited clearance classes. The values apply to non-built-in bearings with zero measurement load.
Contact angle
–
Lubrication
The bearings are not greased and can be lubricated with grease or oil.
Connection with adjacent construction
Positive locking shaft-hub Connection
Full complement cylindrical roller bearings
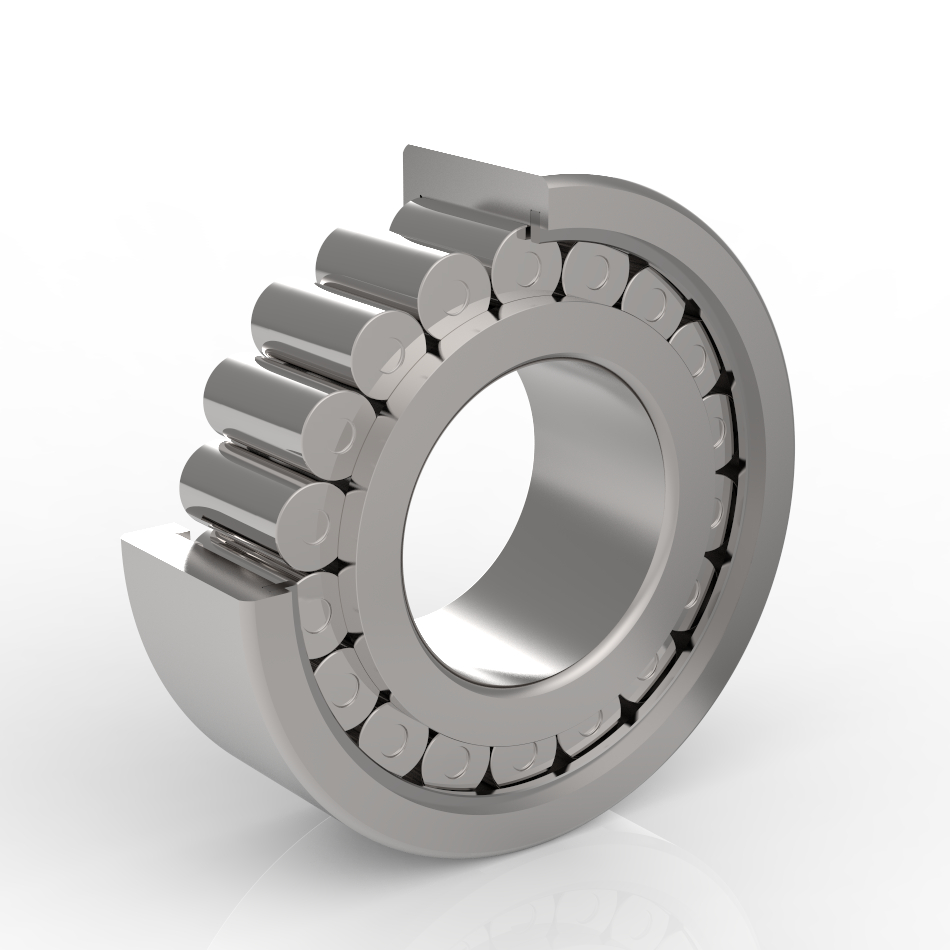
Single row full complement cylindrical roller bearing in NCF design
Full complement cylindrical roller bearings have no cage which keeps the rolling elements apart even in the unloaded zone. Because of the kinematic relationships, full complement cylindrical roller bearings do not reach the same high rotational speed as cylindrical roller bearings with cage.
However due to there being no cage, the greatest possible number of rollers can be housed in the roller bearing. Thus, full complement cylindrical roller bearings can absorb enormous forces; they are very rigid and are particularly suited to space-saving, compact constructions.
Full complement cylindrical roller bearings exist in several designs: single-, double- und multi-row. Especially the multi-row special bearings are particularly rigid, but do not permit any tilting between the inner and outer ring.
Special bearing
- Coated bearing
- Bearings for rope sheaves
- Customer-individual construction
Manufacture sizes
From an outer diameter of 100 mm.
Designs
- Non-locating bearing (purely radial force absorption)
- Double-row: NNCL
- Semi-locating bearing (radial and one-sided axial force absorption)
- Single-row: NCF, NJG
- Double-row: NNCF
- Locating bearing (radial und two-sided axial force absorption)
- Double-row: NNC
Bearing ring materials
Roller bearing steel (Standard)
Rolling elements materials
Roller bearing steel (Standard)
Heat treatments
Martensitic hardening (standard), bainitic hardening and case hardening
Cage materials
–
Main dimensions
–
Dimensional and running accuracy
We manufacture full complement cylindrical roller bearings of tolerance classes normal to P5 as per DIN 620.
Bearing clearance
We manufacture full complement cylindrical roller bearings with radial bearing clearance C2, normal, C3, C4 and C5 as per DIN 620-4, up to individually limited clearance classes.
Contact angle
–
Lubrication
The bearings are not greased and can be lubricated with grease or oil.
Connection with adjacent construction
Positive locking shaft-hub Connection